DIY FSJ Fan Shroud
Return to Home
Return to Resources
Return to FSJ Page
I visited the local metal supply store and purchased 24x36" 0.09" thick 5052 grade aluminum sheet for $27. This sheet is plenty to make a decent fan shroud. I made measurements of the shroud in my Wagoneer and was able to make a new aluminum fan shroud for my J10 in about 3 hours with no special metal fabrication tools. All you need is a jigsaw with a metal blade, a drill, vise, rubber mallet, and a metal file.
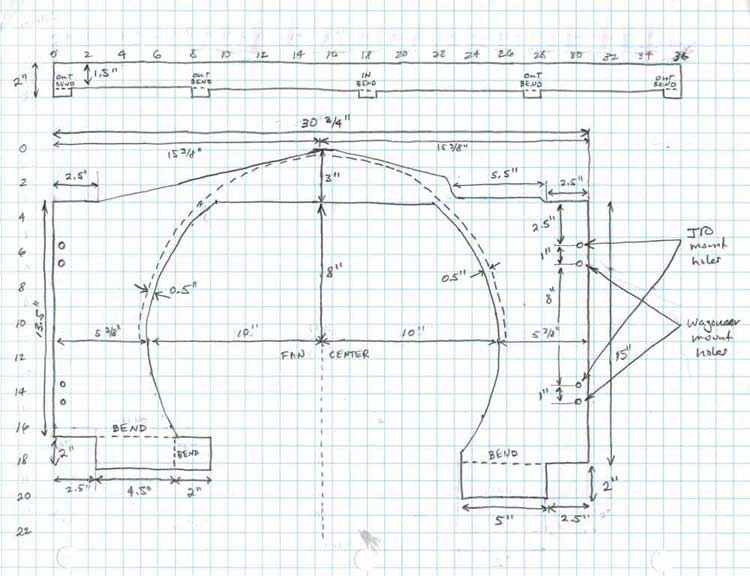
Basically the fabrication steps are:
- Transfer the measurements and cut lines from the drawing to the aluminum sheet. The circle can be drawn easily using a sharpie attached to a string with the other end held down in the center to make a big poor man's compass.
- Use the jig saw to make the cuts. The notch on the upper right is necessary to make room for the upper radiator hose if the shroud is mounted on a Wagoneer because the body is about 1" lower than the J10. If using on a J10, the notch isn't necessary. The radiator mount holes are also 1" lower for the Wagoneer than the J10 as I indicated in the drawing. Then use the metal file to smoothen the cuts and remove all burrs.
- The lower portion of the sheet metal mounts in a vise to make the bends along the dashed lines with "BEND" shown in the drawing. You'll want the top of the vise to be about 1/8" below the bend line to account for some curvature of the aluminum. 0.09" thick sheet is pretty stiff to bend by hand, so I used a rubber mallet to push the sheet over the vise 90 degrees and flatten the bend line as much as possible.
- The 1.5" strip that wraps around the fan has five 0.5" height 1" wide tabs that are bent 90 degrees on the vise. When making the vertical 0.5" cuts for the tabs, overshoot the corner point by about 1/8" so when you put the tab in the vise, you actually will want the top of the vise to be flush with the bottom of the strip so when you bend the tab, the bottom of the tab is flush with the bottom of the strip rather than sticking out about 1/8" or you'll have a small gap all around. The center tab is bent in the opposite direction of the outer 4 tabs.
- Gently bend the strip in the curved shape of the fan; about 21" diameter. The cutout is sized to be about 1 inch narrower (20") as shown in the drawing so the strip is mounted about 0.5" past the edge of the cutout.
- Drill the holes through the tabs of the strip to the shroud plate and mount screws. I used size 8 screws with lock nuts.
- On the back side, I used an aluminum angle bracket that you can get from Home Depot, cut it to 25 inch length and mount it so the flat top of the bracket lines up with the top corners of the shroud. It needs to be centered so there's at least 2.5-3" of spacing from the corners so it doesn't get in the way of the radiator mounts.
- Drill the radiator mount holes as indicated in the drawing. I used the biggest drill bit I had that was at least 3/8". There's only about 0.25" of metal from the edge to the hole. I drilled a couple small pilot holes and then used the larger bit to make the oval notches. No real precision is necessary.
The 1.5" strip doesn't need to go all the way to the bottom half of the shroud. The factory shroud didn't have any lip past that and the reason is because the radiator mount and fan are tilted such that the blades are already partially in the flat part of the shroud at the bottom half. You could go all the way around if you want, but I didn't see a need to go beyond what the factory did.